Industrial and manufacturing, Industry insights, Science + Technology
It could be easy for a contractor to miss - that one line specification that says, "FM Global job," especially for those unfamiliar with FM Global. Despite a client base of Fortune 500 companies, FM Global is not widely known in our industry among developers, design firms and contractors.
That's why we invited Michael Petrie, Operations VP, Operations Chief Engineer with FM Global and Jake Williams, Associate Partner with ATA Beilharz Architects, to join Pepper Project Director Brian Lensink and speak at our inaugural Visionary Series event. The Visionary Series was created to bring in thought leaders to educate owners and industry partners on forward-thinking topics that are helpful to their businesses beyond a single project.
At Pepper, we've completed several FM Global projects and are working on another build out now that will house one of their major clients - a major e-commerce provider. We are impressed with the company and wanted to make our industry more aware of what they do. The topic was timely, given the California wildfires, and since then, the 7.0 earthquake in Alaska.
What is FM Global?
FM Global is a mutual insurance company, owned by their clients. With 67 offices worldwide, they insure 35 percent of Fortune 500 companies, which impact both local and global economies. The company focuses on staffing strategies to build and maintain those relationships. In fact, they don't employ actuaries, but instead have 1800 engineers on staff and base their rates on specific location risk, research and testing.
Established 183 years ago, FM Global brought together like-minded mill owners around the idea that if they made changes with how they run and protect their plants, it should result in lower rates. So unlike their competitors, their labs are designed for testing different materials under extreme conditions.
The difference between FM Global and code compliance
Michael started the discussion with a question: Which facility is cheaper to insure - a hospital versus a warehouse or manufacturing facility? The answer: a hospital. Why? Hospitals have sophisticated systems, like life-safety, that are designed to weather emergency and catastrophic events.
He went on to explain how FM Global approaches the insurance process by exposure-driven engineering, with the goal of building better facilities designed to withstand events, and thus pay lower rates. As such, FM Global approaches different markets based on their location, what they do and the risks they face. Over time, they've learned that clients are five times more likely to suffer a natural hazard than a fire. And most will experience a flood of only 1-2 feet of water, which can take down their operations.
This serves to demonstrate the difference between building code and FM design guidelines. Codes are primarily focused on life-safety and occupant egress. They don't prioritize the costs of property loss or the downtime associated with recovery from a loss event. FM Global, on the other hand, considers the importance of protecting both the occupants and the building operations. Because they design for the whole life of the building and its resilience in the face of disasters, their approach has led to them working with the FDA, NFPA and the Army Corps of Engineers to recommend products to clients and guide the development of additional standards for facility construction. If a company is located on the east coast, they consider exposure to hurricanes, water, and higher wind forces. If on the west coast, they consider exposure to fires and seismic events. If a client should be affected by such an event, it is the use of FM’s more stringent construction standards that help minimize losses to the facility, product, or time in operations.
FM makes their construction recommendations in an effort to mitigate risk or exposure to claims. The owner further decides which of these recommendations to implement by weighing their risk tolerance against any additional construction costs. A building feature is therefore either FM compliant or it is not. Unlike LEED©, there are no point system ratings (certified, silver, gold, etc.), so be sure to understand in an FM constructed facility exactly what features have been designed to their standard.
How does FM Global impact design and construction?
FM Global's approach is based on location-based engineering and engineering resilience into the structure, even as simple as ensuring HVAC systems are screwed together and screwed down. And those standards have paid off for them and for their clients. When Hurricane Katrina hit, FM Global insured more businesses in New Orleans and the greater Mississippi area than their competitors, and yet their losses where half that of their competitors.
When considering an FM Global facility in a hurricane prone region, it's important to understand their model is based on the systems working together and not by themselves. So when a client requests an FM Global roof, whether they explicitly request it or not, they may also be required to install hurricane-resistant windows to meet FM Global's enclosure standards.
Though FM Global has a series of tables to help determine the needs of the building, it's helpful to have an upfront discussion before heading down a specific path because exceptions can be made. For example, there is not an FM-approved ballasted roof, but pharmaceutical and food companies don't want roofing penetrations. It's in their best interest so FM Global will weigh the specific risks for each client and consider alternatives that would be acceptable.
In preparation for the Visionaries meeting, Brian did some cost analysis of FM Global requirements. He found that they may require roof modifications or different sprinkler and fire suppression systems that add a few more heads and bigger pipe sizes, but from a cost and timing perspective, the difference is negligeable. For example, from a roofing perspective there are different levels of construction. FM60 is most closely aligned with a spec building, while FM90 provides greater resistance. The cost difference between the two is maybe 5 percent - not hundreds of thousands of dollars. Further, larger buildings can translate to economies of scale. In fact, the cost increase is seen most often in the additional fasteners.
Tips for engaging FM Global in the process
As I mentioned, each building is treated independently, and since there is no perfect process for working with FM Global, when their standards are specified, it's important to understand how they work - because as we learned from Michael, there is reasonable flexibility to ensure the standards work for the end user's business.
Closer communication - First, FM Global is better engaged when there is a tenant because it requires knowing the products that will be housed there. Further, very often developers and teams are in a competitive situation where they're trying to put together a dollar amount. They make a request to FM Global, who generates a letter of review based on an ideal situation. The process should have more communication and involvement between the design group, construction manager and trades, and with the FM Global account team.
Early involvement - Instead, Jake recommended that the minute the client has an idea of the site, program and building size, the team should engage the FM account manager and find out what they expect to see. Start early-on. When the account teams are engaged to develop a project service plan, they can visit other client buildings and sites, learn more about the exact specifications to which they should design, considerations to think about and even how they respond if there is a unique situation or a disagreement in what is specified. Michael acknowledged that their recommendations should depend on the value to the end user.
Client involvement - Clients trust the design and construction team to know our stuff, but sometimes we need to get them involved for their own benefit - and particularly with an FM Global facility. They may be initially reluctant, but at the end of the project, they understand better what takes place in the process and can help control costs. FM Global's review letter requires owner decisions, and their upfront involvement keeps it from turning into a change order process.
What about spec buildings and developer-driven construction?
For spec buildings, it's harder for FM Global to be engaged specifically. Some of the areas they start with include the building envelope, fire protection and water supply. Water supply is less of an issue with offices, where warehousing is very different. Michael recommended learning more about the available supply directly in front of the building and designing to that.
It's also important to determine who carries the insurance. The developer or the tenant? Sometimes FM Global insures the tenant but not the building owner. Sometimes the policy is direct, brokered, shared or layered.
How product innovation affects the building
New technology presents unknowns and new challenges, and that's where FM Global is well positioned to help their clients. It's also important that we in the design and construction industry understand the implications.
A relatively new industry is additive manufacturing (3D printing). Clients are printing complex parts found in the aviation and power generation industry. Though there may be a premium for the new equipment, clients are drawn to the number of hours that are saved from these newer processes compared to traditional
Lithium-ion batteries have been around for a while now, but they are also considered a finite resource. In fact, it's hard to find. Michael explained the process and cost of testing the material with the NFPA - to figure out how it burns. It was difficult to get a single pallet of material and extremely expensive. Design and construction firms, like us, who work with automotive clients will see the lithium ion battery packs, and it's important to understand the implications on their operations as a result.
Why FM Global's approach matters
Whether or not you believe in climate change or global warming, the fact is we're seeing more frequent and more severe weather conditions. We can argue the cycles and reasons why. However, one factor in the resilience of our buildings is the amount of development taking place in areas that haven't been developed. When it rains, where will the water run? And as other buildings pop up around previously isolated structures, it's crowding the existing systems.
That's why FM Global looks at risk based on geographic area, land contours and other specific factors. The more we understand this, the better we'll also be able to protect and advise our clients. At the close of the Visionaries event, Michael made a simple statement but one worth thinking about: If FM Global doesn't insure it now, eventually they will - because building owners sell to others. Buildings change hands. It's important to consider not just your current tenant or your current structure but what's next.
About the Author
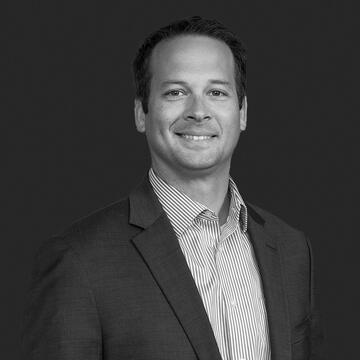