Industrial and manufacturing, Future In Focus
Future in Focus
"Despite a pandemic, we've maintained some pretty stringent schedules that required we not miss a beat. Everyone had to rethink how we do things and to respond daily to different restrictions. The past several months have proven our ability to adapt." – Dan Peddicord, Indiana Vice President
As the entire economy stopped to see what would happen amid COVID-19, the industrial sector paused only briefly. Deemed an essential business, the warehouse and logistics industry has continued to operate under increased demand for e-commerce and a shortage of products. News outlets have reported on the status of product distribution and shared stories of road warriors and front-line workers putting in long hours to package and deliver critical goods and supplies. Distribution companies have added shifts and hired thousands of people amid processes that were cracking under the weight of a business climate that seemingly changed overnight. With the increase in demand the need for new and expanded space followed.
Rethinking the supply chain
The industrial market has weathered the situation better than most sectors, but the outlook differs depending on the type of tenant, the customers they serve and how they deliver goods. Those who ship by air, rail and water have all been hit hard, while many parcel carriers and warehouses have remained busy.
As the business landscape continues to change, companies are looking for new ways of delivering goods more reliably and faster. Many were already starting to move operations away from China because of the tariffs, and the pandemic has only accelerated the diversification of their manufacturing operations.
When it comes to product distribution, businesses are investing in storage closer to urban areas and where their customers reside. As lead times increase and shortages remain, the trend toward just-in-time delivery is being reconsidered, and companies are planning to stock larger inventories. Finally, technology is becoming even more important in helping to manage supply chains and gain efficiencies.
Midwest outlook driven by e-commerce
The coronavirus continues to keep businesses and consumers in limbo. Speed to market is a key project driver, particularly in the Midwest, where retailers can reach up to 90% of their customers within two days.
"Initially, we saw developers and tenants put a hold on projects out of uncertainty while everyone took stock of what COVID-19 meant to their businesses. Some developers had deals ready to sign, and the tenant chose not to proceed," shares Keith Dafcik, vice president overseeing industrial work in Illinois and Wisconsin. "As states started re-opening, fears eased and many projects came back."
- Looking at the precast suppliers as a market indicator, when developers started releasing projects, precast production and availability started to reflect an increase in activity, with lead times extending out four to five months again.
- Big e-commerce players like FedEx, Amazon and the major grocery store chains are doing well, while wholesalers have struggled without purchasers like restaurants and schools ordering products.
- As e-commerce experienced the rush of online orders, they didn't have the resources to keep up with loading and delivering product. Their facilities are being adjusted to focus on the last mile.
- Funding has become a barrier for some to proceed with speculative buildings. Developers with capital funds are trying to capitalize on reduced competition and distressed deals.
Because of its location and infrastructure, Ohio has been a hot spot for distribution, and our volume of work over the last five months has remained steady. Project Director Brian Lensink leads Ohio's industrial group and has been responsible for the delivery of key projects in central Ohio. The site remains the differentiator.
"We have an industrial project that was under construction. The developer stopped progress on the speculative building and is now creating a build-to-suit. The shell was done, and they had to remove a small piece of the shell to retrofit the building for the tenant's operations. Another project was negotiated during excavation and will be modified to suit the tenant's needs. In central Ohio, square footage is getting snatched up as quickly as foundations are laid," explains Lensink.
The cost of industrial construction
"We have seen early signs of potential changes in pricing, more as a result of the overall construction climate than a reflection of what's going on in the industrial market," shares Paul Riehle, preconstruction project executive in Indiana. "But we're not recommending clients hold out for better pricing. Trade contractors are still busy so we have not seen prices come down, and we don't know that they will."
Materials and Supply Chain |
As a result of COVID-19, in addition to precast and steel, we've experienced longer lead times with other systems and materials, like light fixtures, P-Tap, square gear and electrical panels, due to factory shut-downs and delays importing from overseas. Even products from Canada have been slowed at the border. Our teams are closely tracking shipping, creating contingency plans and looking for healthier materials. |
Manpower |
Right now, availability of manpower is not an issue. As new safety and security measures become common practice, productivity is also returning to normal levels. The increase in demand and potential for some workers to elect not to return to the workforce could create a shortage of manpower. |
Competition |
While we are seeing more trades submit quotes, resulting in a wider spread based on trade availability, we have not seen major changes with pricing. Most trades had a backlog through which they have continued to work. As those projects end in the coming months, we may start to see lower prices. |
Finding more productive ways of working in a COVID-19 environment
Developers have expressed concerns about maintaining productivity on their projects under new guidelines. Orientations that address COVID-19 measures, temperature screenings, disinfecting tools, wearing face masks and social distancing all add extra steps and time – for businesses that can't get their spaces turned over fast enough. Fortunately, our industry has already learned to adjust – and in the process, we've found better ways of working post-COVID-19.
The floors are critical to the performance of a distribution center and typically require a highly orchestrated process that involves trades working shoulder-to-shoulder. Productivity and timing are key to achieve proper curing. We wondered if it was even a possibility to spread out.
"At first, we weren't sure if we could continue with the concrete operation; we thought we would have a problem because of social distancing," explains Peddicord. "In addition to the challenges of following new guidelines, masks were in limited supply and some people were not working because of the risk to their health or having already been exposed to the virus."
Together with our industry partners, we implemented several measures to improve the working environment while ensuring no productivity was lost:
- Crews altered how they placed the concrete so fewer workers were in close proximity to each other.
- Workers that still had to work within six feet of each other wore KN95 masks, which are similar to the N95 masks but not rated for medical use. This allowed us to achieve our purpose without using the scarce resources needed by those on the front lines in the medical community.
- Even the KN95 masks were in short supply so we bought a UV-C disinfecting lamp to sterilize surfaces. Each person had two masks that could be alternated while one was being disinfected, allowing us to get more life out of the disposable PPE.
- Deliveries were adjusted so instead of truck drivers getting out of their vehicles, putting the shoots in place, dumping the concrete and washing off their equipment before heading back to the batch plant for another load, two workers are located on-site to set up, pour the concrete and clean the equipment. The driver stays inside the vehicle.
- Concrete for large projects that previously was supplied by 2 or 3 plants was coordinated so all trucks were routed from the same batch plant.
- The finish trades assigned workers to small teams to keep the same tradespeople together and contain the potential for spread.
By implementing these measures and re-prioritizing some activities, we didn't experience any project delays. In fact, we just turned over a 600,000-square-foot facility on time, despite all of the concrete pours taking place during the pandemic. It was a condensed schedule to begin with, and we still achieved it.
Peddicord concludes: "We've found there are ways of working that we'll continue because it's more cost efficient, makes our operation more efficient and creates a better work environment. We weren't actively seeking those improvements, but they've happened as a result."
Bringing the future of industrial construction into focus
The industrial market has historically trailed other industries when it comes to incorporating new systems and ideas into their buildings. Not even five years ago, developers were still specifying incandescent lighting and debating who should cover the cost. Today, LEDs are standard, and cost is no longer a factor.
That's why, as we anticipate how COVID-19 will impact future buildings, it's ironic that the warehouse and distribution center designs already have an advantage.
Higher performing buildings
So how is the industrial sector adapting their buildings to better prepare for the next event – or even the next wave - while providing safe and comfortable work environments that keep their employees healthy?
-
Industrial buildings are good candidates for solar roofs. - Solar Power - One newer system that was gaining attention before the pandemic is the solar array, which works well on the flat, expansive rooftops and offers several advantages to the building's operations beyond energy savings. Buildings that need to maintain a cool environment are particularly good candidates.
- Material Supplies – In the future, it's expected industrial companies will pay more attention to the materials used in their buildings, both tracking their origin to prevent shut downs in the supply chain and finding opportunities for cost savings through bulk purchases.
High Performance Project Manager Evan Caprile explains, "Buying in bulk, when possible, is a smart business decision, and it benefits the environment by reducing handling, packaging materials and waste."
Using technology for communication
More than anything, remote working has reinforced the tools we have today as an effective way of facilitating progress amid other limitations. Industrial spaces don't require the most advanced technology to build so as we think about the tools we use, we focus on communication and visualization.
The example above of a 4D schedule is one technology that teams have leveraged more while working remotely. It gives developers the ability to share the schedule with their prospective tenants in a visual way and from any location. For us, 4D schedules have helped with sequencing and logistics, particularly when multiple buildings are in progress.
"By putting all of the durations together for all the buildings in an industrial park, I could see how the logistics and sequencing would work and what it would take to build from a high level," comments Dafcik. "That model can also be referenced during construction."
What's next with industrial construction
In the future, in addition to changing how we work, tracking labor shortages and identifying upfront where we may have issues can help us cost-load models and look at labor on a different level to account for these concerns during the planning phase.
Pre-COVID-19, developers were setting the stage for increased flexibility. Instead of developing a site for one building, maybe with the potential to add another facility in the future, they were planning for more variety – multiple sizes with different configurations and the ability to offer all on day one. Inside, clear heights extend 40 feet with more variables for dock positions and doors per square foot, as well as rough-ins for offices. These features haven't changed, but like other industries, we are expecting to see designs evolve as they adopt new ways of operating.
This blog post is part of the Future In Focus series, which analyzes the decision to proceed, as well as the creativity and tools to wisely manage your project. Experts from across the company are weighing in so you can start to sort through all the unknowns and make the most informed decisions possible. We encourage you to subscribe to our newsletter to receive updates.
SIGN UP TO RECEIVE UPDATES
About the Authors
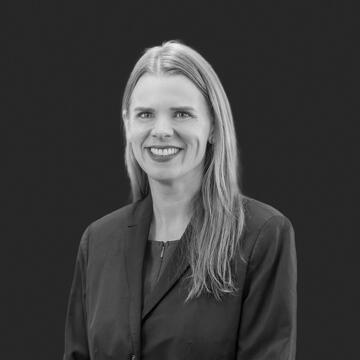
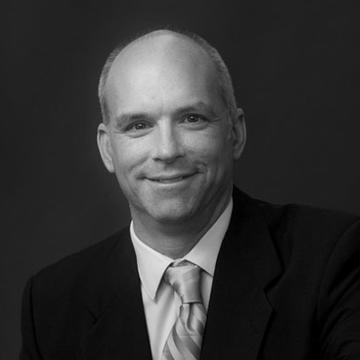
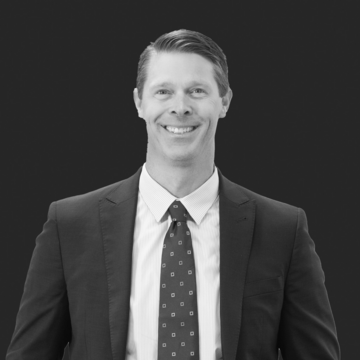
