Virtual construction & technology
How a building operates after a contractor turns over the keys is just as important as the design and construction process. At Pepper Construction, we have worked with a number of owners on delivering a product that either works with their current Computerized Maintenance Management System (CMMS) or helped create a plan and process for a new Facility Management solution that fits their needs. Every owner’s goals, staff and facilities are different, so it’s important to understand where the owner is today, and where they want to go.
Benefits of a Building Information Model (BIM) to FM Solution
There are many reasons to use BIM for facility management:
- Improved space management and communication of information
- Increased efficiencies and streamlined facility management
- Better understanding of operational and maintenance costs and usage with increased opportunities for energy and operational savings (ROI & Life Cycle Management)
- More accurate and complete as-built documentation for maintenance and future renovations
How clients are currently building FM solutions
For those considering a facility management solution, it's important to understand no solution is the same for everyone, and the process can vary depending on where you are in your journey. These are just a few examples:
At Northwestern’s Outpatient Care Pavilion in Chicago, Northwestern had an established set of goals and guidelines for their Facility Management needs. Pepper utilized a combination of digital and physical asset tagging to provide additional information at turnover for the owner's facilities staff. Different elements within the 3D models were tagged with specific identification and hyperlinks that could be chosen via iPad or web. Those hyperlinks provided access to the model and would bring up information about a particular item, such as service and product information, as well as any other COBie data that was required for the project. The specific IDs were also physically tagged on the elements in the field for consistent identification.
At Columbus Regional Hospital in Columbus, Indiana, the owner wanted a master model they could use as the source and standards for their operations. Before the model was created, Columbus Regional Hospital invited Pepper and the rest of the team to a two-day lean “value stream mapping” process. The hospital wanted to see how the design team and construction team develops the model and also wanted the project team to understand how the hospital uses the data from the model for their campus operations. Together they developed a process to deliver the model and data in a way the hospital could use the information moving forward.
The resulting solution was flexible to allow the hospital to choose its own software platform at a later date and specific enough to establish standards and processes that would work for their current project and all future projects. Duplicate and wasteful steps were eliminated, streamlining the process to save time and cost. Since the hospital didn’t have a specific facilities management software in place, having the conversation upfront about how the hospital would use the data from BIM allowed Pepper to create the model in a way that solved current project challenges while also gathering and delivering the data in a way that would work with any software they chose. Pepper played an integral part in managing the COBie data for the project, as well as tying those assets to the 3D model.
On the Butler University Chilled Water Plant project, the owner wanted a simple and flexible solution for taking project information into their CMMS platform at the end of the project. They also acknowledged their CMMS system may change in the future and wanted a deliverable solution that would be flexible regardless of the CMMS chosen. The solution: a customized COBie spreadsheet.
At Neuro Diagnostic Institute Tower/Family and Social Services Administration, the owner wanted to take full advantage of the design and construction models being developed as part of the project, and they asked us to help determine the appropriate solution for them based on their facilities management goals. We are currently working with them to develop their FM solution using a platform called EcoDomus. This cloud-based tool will combine all of the design and construction models into an easy-to-access platform where all of the building’s asset information, O&M information and documents are stored. The models will also contain information about replacement cost for all equipment within the building so they can report back to the State of Indiana. Finally, their facilities staff will use iPads to access EcoDomus in the field – allowing them to be as efficient as possible when accessing data and drastically reduce work order response times.
Like these clients and others, many are expressing interest in a deliverable that will help them through the life of the building. We're also seeing more owners ask for information about facility management solutions as part of the Request for Proposal (RFP) process. With the way Pepper uses the model from the very beginning of design all the way through construction, accounting for energy and lifecycle costs, we're already set up to accommodate these requests. However, the challenge with answering the question in a proposal is there is no one-size-fits-all answer. From the software that is selected to the process of gathering the data and to the data itself, the solution is contingent on many different project-specific factors. And no two platforms are alike. So as an owner, how do you know where to start?
Questions to facilitate the internal BIM FM process
We've identified a process and some common characteristics that help us evaluate and recommend the right solution. Start with the following questions.
- The number one question you should always ask is not, "What data do you want to track?" but rather: "What data do you want to maintain?"
- How are you managing your facility and data today? What systems do you already have in place?
- How much of your building is new vs existing? Of the existing, how much is known and how accurate is it?
- What is the knowledge and skillset of your facility management team?
- How do you want to operate tomorrow?
The right data
We can track anything, but we've found that at some point it becomes too much. Data overload is a real problem today. Some assets are not relevant or become too overwhelming to maintain, both for you to manage and for the contractors providing the information - not to mention it could cost more. To get the most out of your platform, it's important to identify the right amount of data to track and how it will integrate with your system. You should always keep in mind that someone has to update or maintain that data. For example, if there are future renovations, who will be updating the Building Information Model? Will you hire staff in-house? Will you contract out to a third party? If a piece of equipment needs to be replaced, who will update that data in the system? All of this should be considered when outlining what data you want to track. If it's inaccurate, we've found people stop relying on the data.
Additionally, don’t be afraid to go back and re-evaluate the information you are maintaining. At Pepper, we have a list of recommended assets to track. We’ve also had multiple clients request we track fewer assets on a future project than the first project we worked on because they realized they couldn't or didn't need to maintain that information. Finally, the earlier you outline the data you want to track on a project, the better. It always costs more to go back and do something after the fact. If we know early in the project what data you want collected and in what format, we can create a process together that works best for all parties involved.
The right platform
Once you've answered the questions above and determined the data you want to capture, the next step is to identify the right approach and platform that will meet your needs. And there are many out there. At Pepper, we're developing a spreadsheet of all of the options that are out there, to help us keep track and make recommendations based on different owner criteria. No single solution fits everyone’s needs, so knowing what options are available helps meet our clients' current needs and workflows.
The right process
In addition to identifying the right platform, it's helpful to collaborate with industry partners not only to understand how they use BIM, but also so they understand how you need the data delivered so it can be useful for you in the future. If you are simultaneously building the master model while completing a project, your team should set up a process and standards for how the data is collected. Training and education play the most important role in the process, not only for those collecting the data, but for those using the data. Like any process, it’s important to follow lean principals, always reviewing and improving, even throughout intermediate stages of the project.
Worth the effort
Recently, Pepper conducted a trade partner survey about technology. Many of the questions focused on how and why they use BIM. To use BIM for facility management, the trades need to be contributing to the model and organizing data in a useful way for the owner. And while in the past couple of years adoption has gone up and more trades see the value in their own businesses, we also continue to find the primary reason for using BIM is when it's required on a project. Further, when asked whether they have contributed to a facility management solution, an overwhelming majority have not. Of those who have, many qualified their responses suggesting they were not certain the model was being used. Some explained they didn't believe the data they provided from construction was in a useful format for the owner to maintain the building or plan for future work.
Clearly, there is a gap between how the owner needs the data and how it is supplied by the trades. BIM for FM is still an ideal that most desire, and yet it's still rarely used because it's such an overwhelming undertaking. However, there are proven examples and processes that can help you get started, and for those who invest the time, we're seeing clients gain considerable insights into how to optimize their facilities.
About the Author
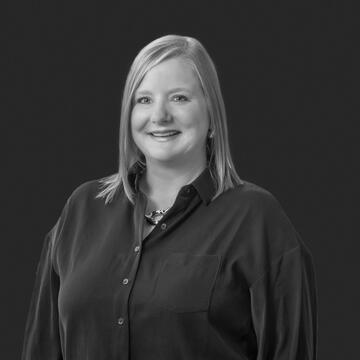